Glass distortion is inherent and accepted within the glass manufacturing industry, to a point. To many, this may come as a shock, but as we take a closer look at glass manufacturing processes, and outside mitigating factors, you’ll discover both the true benefits and outside causes that dictate the level of distortion you may or may not be perceiving. As we dive in we will touch on answering a few questions to help build a better understanding:
- What is glass distortion and how is it caused?
- Has glass distortion always been this prevalent?
- Is there an industry standard for inherent glass distortion?
What is glass distortion and how is it caused?
Glass distortion is any abnormalities that are perceived by the eye of warped, wavy, or rippled high or low points of glass. These peaks and valleys of the glass create optical distortion and may be viewed easier from different angles or distances from the glass. Additionally, these distortions are more prevalent in heat-treated and tempered glass compared to annealed glass (non-treated). The most common type, and still considered a minor level of distortion, is referred to as “roller wave distortion.”
Roller wave distortion occurs in Tempered glass, and/or heat-treated glass, and is achieved through a heating process that reaches around 726 degrees. During the heating process, the glass travels through the furnace on ceramic rollers, while traveling, the heated glass can slightly sag between rollers causing roller wave distortion. The outer surfaces are then rapidly cooled, twice as fast as heat-strengthened glass, with the inner core cooling relatively slower. This creates tension between the surfaces putting them in a constant state of compression. The compression created from the outer glass, in combination with tension from the inner glass, makes the glass more resistant to breakage while adding the desired strength and safety associated with tempered glass. This effect gives tempered glass nearly four times the strength of annealed glass. Roller wave distortion is caused by the manufacturing process, is not considered a defect, and is inherent to all tempered or heat-treated glass.
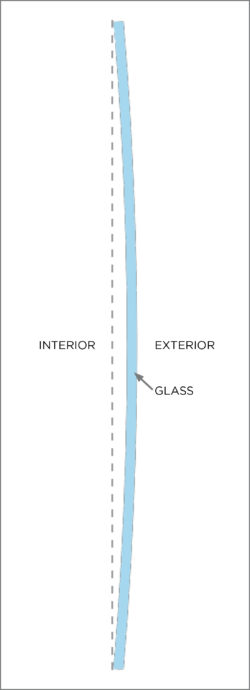
There are two other more natural factors that create glass distortion: location and climate. With locations, the atmospheric pressure found at higher elevations can create a bowing effect on panes of glass. For example, sealed insulated glass assembled at a lower altitude than the location of installation can cause the panes of glass to bow outward. As a first step in the window ordering process, building site elevation is determined to decide if Altitude Glass is required to mitigate this bowing effect. The second natural cause is climate, where temperature fluctuations caused by changing seasons or the time of day and other environmental elements can create modest glass distortions.
Lastly, odd-shaped windows or narrow glass panes are more likely to be susceptible to bowing or warp distortion, so keep this in mind when planning your window and door sizes and proportions.
Has glass distortion always been this prevalent?
In short, not exactly. As building standards and codes become more stringent, so do the performance standards on glass. “Low-E” coatings (low emissivity coating) were introduced as a method of reflecting solar heat back to its source, creating a building that is more thermally comfortable and better suited to meet or exceed, building performance requirements. However, with the increase in reflectivity (read: performance) optical distortions became more detectable, which in turn increased the ability to perceive the inherent distortions of tempered glass.
Is there an industry standard for inherent glass distortion?
As of now, no. Although the strength of tempered glass must meet specified requirements under ASTM C1048 (American) and EN12150 (European), the distortion that occurs due to the process is not standardized. However, each window manufacturer holds its glass to its own standards in order to ensure that only glass with the highest clarity, quality, and performance leaves the manufacturer’s floor.
ASTM and EN recognize that glass distortion is inherent to the production process and concedes judgment to the glass industry. Glass manufacturers’ goal is to minimize roll wave distortion and use different tools in order to measure and monitor distortion.
One common tool is called the “Statistical Process Control Tool” which measures the waves with a gauge. The Millidiopter gauge is able to discern, with a high-powered lens, the amount of curvature present on the glass surface. The higher the millidiopter reading is, the greater the curvature and the greater the optical distortion. A generally accepted reading for tempered glass is +/-298 millidiopter of distortion with a roll wave of .008 (although this number may vary from manufacturer to manufacturer). For a full breakdown of European ranges of tempered glass and surface compression, please read the full report here.
So, although glass distortion is inherent to all tempered and heat-treated glass, and made more visible with Low-E coatings, the end product becomes a harmonious balance of performance and limited optical abnormalities.